Many anglers either know first hand or have heard of the many benefits that fluorocarbon fishing lines offer. But not much is known about how these fantastic fishing lines are made in the first place. So keep on reading as we pull back the curtain behind how fluorocarbon fishing lines are manufactured.
Fluorocarbon fishing lines are produced from a plastic called polyvinylidene fluoride (PVDF). The PVDF plastic pellets are melted down and extruded through a die containing holes. The line is then cooled to a certain temperature and stretched out to rearrange the molecules for greater strength.
The materials used to make fluorocarbon line and the manufacturing process gives the line characteristics that make it perfect as a leader line. But, many anglers do use it as a mainline as well. Let’s take a deeper dive into how fluorocarbon lines are made.
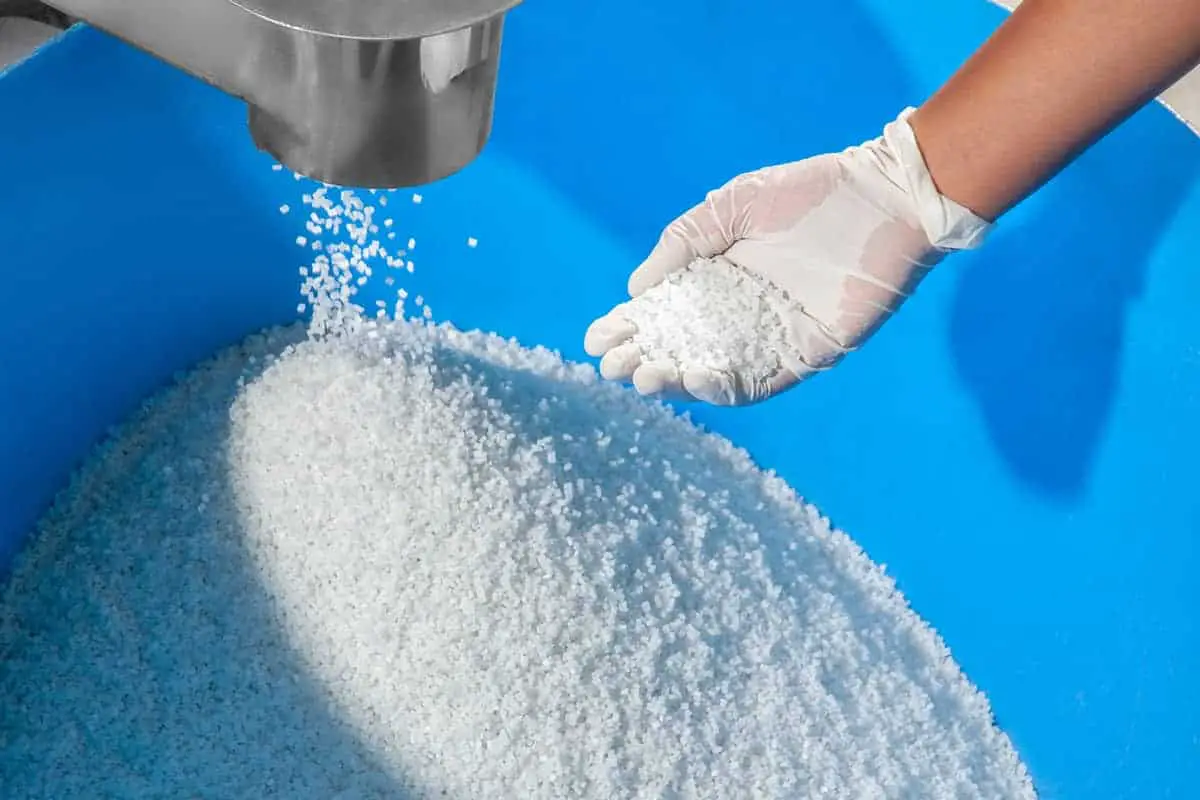
A Deep Dive Into The Manufacturing Process For Fluorocarbon Line
The manufacturing process used to make fluorocarbon fishing lines can be generally described as:
- Extrusion
- Filament Forming
- Orientation
- Annealing
- Winding
If you are familiar with how monofilament fishing lines are manufactured, then the process is very similar. But for those of you who are not familiar with the process, let us break down each manufacturing process in more detail.
1. Extrusion
PVDF plastic pellets are put inside a heated hopper, where the pellets are melted into a thick and viscous liquid. The liquid plastic runs down into a chamber where a mechanical plunger pushes the liquid through a die.
The die is made from metal and will have a series of holes all over it. The holes could be the same or different sizes – that depends on the company. When the liquid plastic gets pushed through these holes, a continuous fluorocarbon line is formed.
The hole diameter from the die develops your fishing line diameter.
Adding Addivitives To Change Certain Charactertisitics
Many fluorocarbon line manufacturers add various resins and other materials to the line to enhance its characteristics. Many of these products added are trade secrets that are not revealed.
But we know these products are mixed in with PVDF in the heated hopper.
The addition of resin to the PVDF can increase abrasion resistance and flexibility and reduce degradation from UV exposure and memory.
If your fluorocarbon line has any colour, then this is the stage where colour is added. Coloured dye is added to the heated hopper and blended with the liquid plastic to give it its colour.
2. Filament Forming
After the liquid passes through the die, it’s immediately cooled down through a quenching bath. This allows the plastic to form its molecular structure, giving it some strength to withstand the remaining manufacturing processes.
The temperature of the cooling liquid in a quenching bath is typically maintained between 104°F (40°C) to 194°F (90°C).
Once the fluorocarbon line is cooled through the quenching bath, it then goes through a dryer to remove the moisture from the line before it goes to the next stage in the manufacturing process.
Adding External Coatings To The Fishing Line
If there is going to be an external coating applied to the fishing line to provide more abrasion resistance or protection against UV exposure, it would be added to the quenching bath’s liquid.
As the line enters and exits the cooling liquid, it will get coated with this product and cured throughout the manufacturing process’s remaining.
3. Orientation
The molecular structure formed in the filament-forming process was random, which means that the molecular structures have no formation or orientation. The orientation of the molecular structures is what gives the fishing line its strength.
To reorient these molecules, the line will be placed under high tension. Stretching out the line while the line is at a certain temperature will allow the molecules to rearrange themselves in the direction of the pulling force to resist the pulling force.
To accomplish this, the fishing line has to pass through one or more rollers and heaters.
The rollers will rotate at slightly different speeds, creating the tension force needed to rearrange the molecules.
The heaters are needed to keep the line at a certain temperature to rearrange the molecules between different rollers.
4. Annealing
This stage aims to remove the stresses in the fishing line that was developed in the orientation stage.
This is accomplished by slowly heating the line to the proper annealing temperature. This can be done through an oven or liquid bath.
The tension applied to the fishing line during this step is reduced. There is enough tension applied still to keep the line firm. This will prevent the line from shrinking as it cools. This will prevent the molecules stretched and rearranged during the orientation process from returning to their original orientation before they were stretched.
5. Winding
This is the final stage where the fluorocarbon fishing lines are wound up on individual spools.
These spools are what will be sent out to stores for sales.
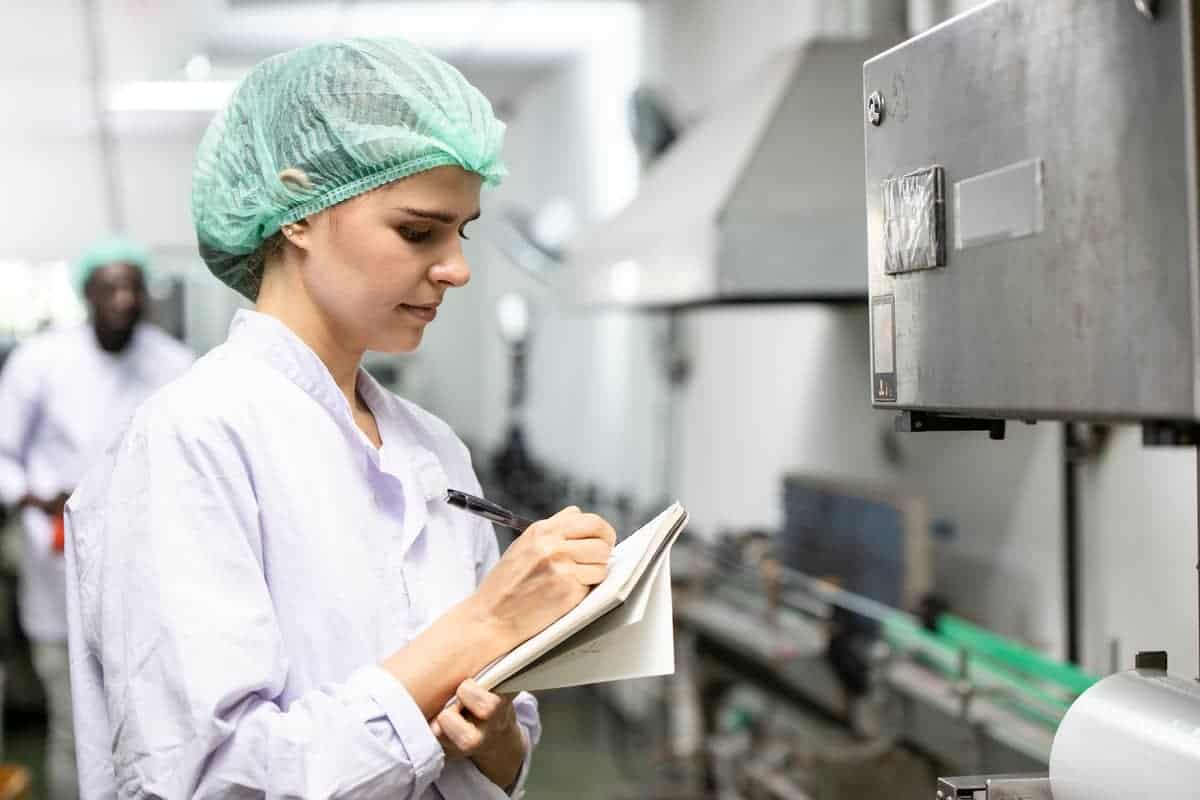
Quality Assurance And Testing Of Fluorocarbon Lines
All fluorocarbon line manufacturers put their lines through rigorous testing to check the line’s quality and make sure it meets specifications.
Companies such as Seaguar produce different classes of fluorocarbon lines intended for different types of fishing. Each line has different materials added to give each type of line the specific characteristics needed for certain applications.
Each batch of fluorocarbon line is tested in the manufactures quality control departments for the following qualities.
- Breaking strain
- Strength tests
- Knot strength
- Submersion tests
- Temperature endurance tests
- Abrasion resistance tests
How Are PVDF Plastics Pellets Made
PVDF is a type of fluorocarbon polymer which means it’s a plastic formed by combining carbon and fluorine compounds.
This happens by using Vinylidene Fluoride in its gas form as the base monomer. Carbon is then added to the mixture, and it undergoes a process called polymerization, which produces the PVDF pellets used to make fluorocarbon fishing lines.
Diving In Deep On PVDF Materials
PVDF in itself offers certain characteristics over monofilament lines.
The density of the fluorocarbon material means the molecules are packed more tightly together, and the bond between them is stronger.
This tighter bond makes fluorocarbon lines inherently stronger than monofilament. The density of the fluorocarbon also increases the water resistance of the line, so it is less likely to become waterlogged, unlike monofilament lines.
Contrary to popular assumption, fluorocarbon line does have stretch, but it is more difficult to stretch. This feature increases the angler’s sensitivity on the line and allows the angler to feel when a fish is bumping a lure.
The lower elasticity also allows the lure to react more naturally than monofilament, which may exaggerate how a lure reacts to a bump by a fish, causing the fish to shy away.
How Does The Material Affect The Cost Of Fluorocarbon Line?
Fluorocarbon fishing line is typically more expensive than monofilament line. This has nothing to do about the quality of the product but has everything to do with the difference in costs of the raw materials to produce the fluorocarbon line and the higher temperatures required when making the line.
The process used to make a monofilament line is quicker and less complex than the processes used for a fluorocarbon line.
Because of the higher cost, anglers typically use fluorocarbon lines as leaders. However, in some applications, anglers do use certain types of fluorocarbon lines on their reels.
Is Fluorocarbon Fishing Line Environmentally Friendly?
Fluorocarbon is a manmade plastic-type product, which is not environmentally friendly. The material used to make fluorocarbon lines will not break down quickly in the environment.
Consequently, you should avoid leaving fluorocarbon lines in the environment wherever possible. This is also true with monofilament lines, which also do not degrade quickly in the environment.
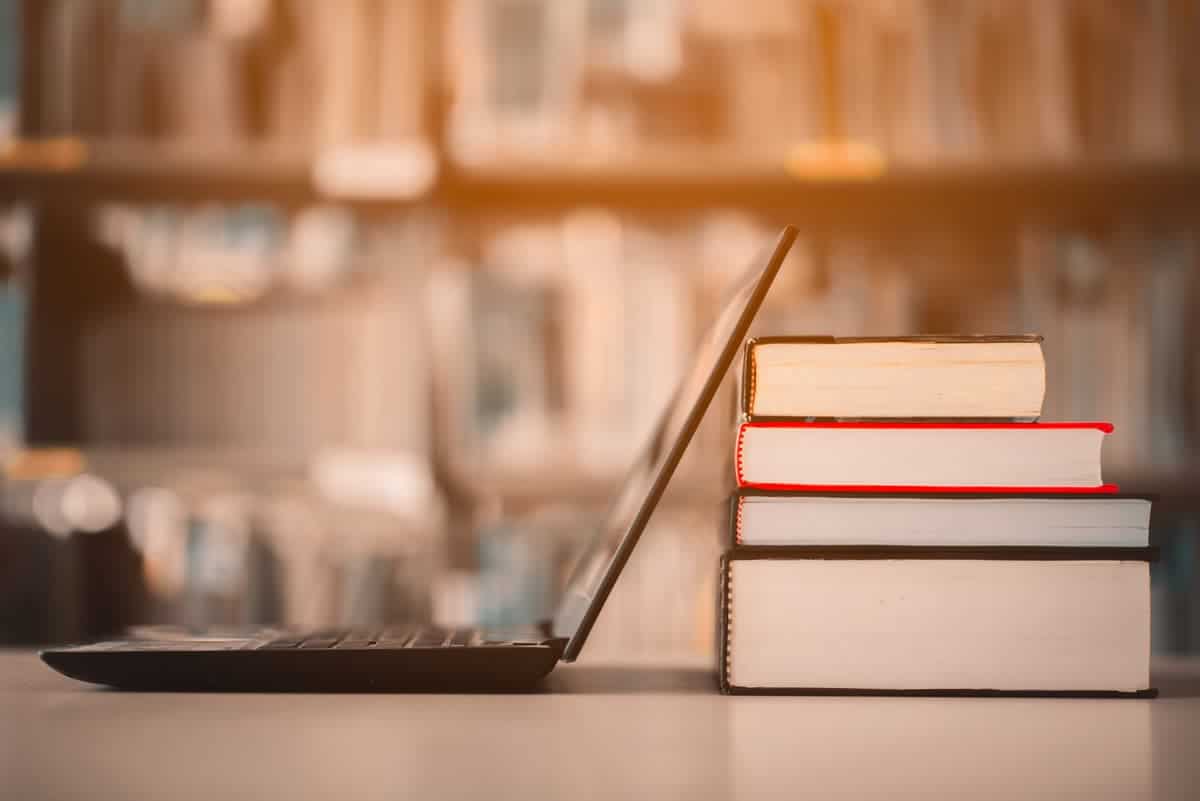
Histroy of Fluorocarbon Lines
Fluorocarbon line is not as new as many people think. This fluorocarbon fishing line has an interesting history and has been around as early as 1971, but the materials and manufacturing processes have changed since those days to give us the fluorocarbon lines we have today.
Back in the day, fluorocarbon lines kinked very easily, and cold weather made this problem even worse!
Because of this, there are a lot of misconceptions behind Fluorocarbon lines today. Many of these issues have been greatly reduced from modern manufacturing processes.
Development of New Fluorocarbon Lines
Fluorocarbon line makers are constantly working to improve their products and introduce additional qualities to improve performance.
Fluorocarbon line manufacturers set aside large budgets to undertake this research and development to bring new and improved fluorocarbon lines to the market.
The research can involve blending other ingredients to change characteristics, combinations of heating, cooling, pressure, and tension to change the material’s properties.
Seaguar, the founder and inventor of fluorocarbon line, has recently introduced Double Structure Fluorocarbon, or DSF. The resin is extruded with the PVDF rather than coating the line after extrusion.
This process change improved the bond between the materials and produced a higher quality fluorocarbon line, with superior characteristics for saltwater fishing.
Happy Fishing & Tight Lines